Product Description
Stainless steel welded pipes are integral components in a wide range of industries due to their durability, corrosion resistance, and versatility. These pipes are fabricated through a welding process, joining stainless steel sheets or strips to form cylindrical tubes. Here's a comprehensive overview of stainless steel welded pipes:
Materials and Grades:
● 304 and 316 series: Common general-purpose stainless steel grades.
● 310/S and 310H: High-temperature-resistant stainless steel for furnace and heat-exchanger applications.
● 321 and 321H: Heat-resistant grades suitable for elevated temperature environments.
● 904L: Highly corrosion-resistant alloy for aggressive environments.
● S31803: Duplex stainless steel, offering both strength and corrosion resistance.
Manufacturing Process:
● Electric Fusion Welding (EFW): In this process, a longitudinal seam is welded by applying electrical energy to the welding arc.
● Submerged Arc Welding (SAW): Here, the weld is made by melting the edges with a continuous arc submerged in flux.
● High-Frequency Induction (HFI) Welding: This method employs high-frequency currents to create a weld seam in a continuous process.
Advantages:
● Corrosion Resistance: Resistant to a wide range of corrosive media and environments.
● Strength: High mechanical strength ensures structural integrity.
● Versatility: Available in various sizes, grades, and finishes to suit different applications.
● Hygiene: Well-suited for industries with stringent sanitary requirements.
● Longevity: Exhibits exceptional durability, resulting in extended service life.
In summary, stainless steel welded pipes are essential components across industries, providing durability, corrosion resistance, and versatility for a variety of applications. Proper selection of grade, manufacturing method, and adherence to industry standards are critical for ensuring optimal performance and safety of the welded pipe systems.
Specifications
ASTM A312/A312M:304, 304L, 310/S, 310H, 316, 316L, 321, 321H etc... |
EN 10216-5: 1.4301, 1.4307, 1.4401, 1.4404, 1.4571, 1.4432, 1.4435, 1.4541, 1.4550 etc... |
DIN 17456: 1.4301, 1.4307, 1.4401, 1.4404, 1.4571, 1.4432, 1.4435, 1.4541, 1.4550 etc... |
JIS G3459: SUS304TB, SUS304LTB, SUS316TB, SUS316LTB etc... |
GB/T 14976: 06Cr19Ni10, 022Cr19Ni10, 06Cr17Ni12Mo2 |
Austenitic stainless steel: TP304, TP304L, TP304H, TP310S, TP316, TP316L, TP316H, TP316Ti, TP317, TP317L, TP321, TP321H, TP347, TP347H, TP347HFG N08904(904L), S30432, S31254, N08367, S30815... Duplex stainless steel:S31803, S32205, S32750, S32760, S32707, S32906... Nickel Alloy:N04400, N06600, N06625, N08800, N08810(800H), N08825... Usage: Petroleum, Chemical, Natural gas, Electric power and Mechanical equipment manufacturing industries. |
DN mm |
NB Inch |
OD mm |
SCH40S mm |
SCH5S mm |
SCH10S mm |
SCH10 mm |
SCH20 mm |
SCH40 mm |
SCH60 mm |
XS/80S mm |
SCH80 mm |
SCH100 mm |
SCH120 mm |
SCH140 mm |
SCH160 mm |
SCHXXS mm |
6 |
1/8” |
10.29 |
1.24 |
1.73 |
2.41 |
|||||||||||
8 |
1/4” |
13.72 |
1.65 |
2.24 |
3.02 |
|||||||||||
10 |
3/8” |
17.15 |
1.65 |
2.31 |
3.20 |
|||||||||||
15 |
1/2” |
21.34 |
2.77 |
1.65 |
2.11 |
2.77 |
3.73 |
3.73 |
4.78 |
7.47 |
||||||
20 |
3/4” |
26.67 |
2.87 |
1.65 |
2.11 |
2.87 |
3.91 |
3.91 |
5.56 |
7.82 |
||||||
25 |
1” |
33.40 |
3.38 |
1.65 |
2.77 |
3.38 |
4.55 |
4.55 |
6.35 |
9.09 |
||||||
32 |
1 1/4” |
42.16 |
3.56 |
1.65 |
2.77 |
3.56 |
4.85 |
4.85 |
6.35 |
9.70 |
||||||
40 |
1 1/2” |
48.26 |
3.68 |
1.65 |
2.77 |
3.68 |
5.08 |
5.08 |
7.14 |
10.15 |
||||||
50 |
2” |
60.33 |
3.91 |
1.65 |
2.77 |
3.91 |
5.54 |
5.54 |
9.74 |
11.07 |
||||||
65 |
2 1/2” |
73.03 |
5.16 |
2.11 |
3.05 |
5.16 |
7.01 |
7.01 |
9.53 |
14.02 |
||||||
80 |
3” |
88.90 |
5.49 |
2.11 |
3.05 |
5.49 |
7.62 |
7.62 |
11.13 |
15.24 |
||||||
90 |
3 1/2” |
101.60 |
5.74 |
2.11 |
3.05 |
5.74 |
8.08 |
8.08 |
||||||||
100 |
4” |
114.30 |
6.02 |
2.11 |
3.05 |
6.02 |
8.56 |
8.56 |
11.12 |
13.49 |
17.12 |
|||||
125 |
5” |
141.30 |
6.55 |
2.77 |
3.40 |
6.55 |
9.53 |
9.53 |
12.70 |
15.88 |
19.05 |
|||||
150 |
6” |
168.27 |
7.11 |
2.77 |
3.40 |
7.11 |
10.97 |
10.97 |
14.27 |
18.26 |
21.95 |
|||||
200 |
8” |
219.08 |
8.18 |
2.77 |
3.76 |
6.35 |
8.18 |
10.31 |
12.70 |
12.70 |
15.09 |
19.26 |
20.62 |
23.01 |
22.23 |
|
250 |
10” |
273.05 |
9.27 |
3.40 |
4.19 |
6.35 |
9.27 |
12.70 |
12.70 |
15.09 |
19.26 |
21.44 |
25.40 |
28.58 |
25.40 |
|
300 |
12” |
323.85 |
9.53 |
3.96 |
4.57 |
6.35 |
10.31 |
14.27 |
12.70 |
17.48 |
21.44 |
25.40 |
28.58 |
33.32 |
25.40 |
|
350 |
14” |
355.60 |
9.53 |
3.96 |
4.78 |
6.35 |
7.92 |
11.13 |
15.09 |
12.70 |
19.05 |
23.83 |
27.79 |
31.75 |
35.71 |
|
400 |
16” |
406.40 |
9.53 |
4.19 |
4.78 |
6.35 |
7.92 |
12.70 |
16.66 |
12.70 |
21.44 |
26.19 |
30.96 |
36.53 |
40.49 |
|
450 |
18” |
457.20 |
9.53 |
4.19 |
4.78 |
6.35 |
7.92 |
14.27 |
19.05 |
12.70 |
23.83 |
29.36 |
34.93 |
39.67 |
45.24 |
|
500 |
20” |
508.00 |
9.53 |
4.78 |
5.54 |
6.35 |
9.53 |
15.09 |
20.62 |
12.70 |
26.19 |
32.54 |
38.10 |
44.45 |
50.01 |
|
550 |
22” |
558.80 |
9.53 |
4.78 |
5.54 |
6.35 |
9.53 |
22.23 |
12.70 |
28.58 |
34.93 |
41.28 |
47.63 |
53.98 |
||
600 |
24” |
609.60 |
9.53 |
5.54 |
6.35 |
6.35 |
9.53 |
17.48 |
24.61 |
12.70 |
30.96 |
38.89 |
46.02 |
52.37 |
59.54 |
|
650 |
26” |
660.40 |
9.53 |
7.92 |
12.70 |
12.70 |
||||||||||
700 |
28” |
711.20 |
9.53 |
7.92 |
12.70 |
12.70 |
||||||||||
750 |
30” |
762.00 |
9.53 |
6.35 |
7.92 |
7.92 |
12.70 |
12.70 |
||||||||
800 |
32” |
812.80 |
9.53 |
7.92 |
12.70 |
17.48 |
12.70 |
|||||||||
850 |
34” |
863.60 |
9.53 |
7.92 |
12.70 |
17.48 |
12.70 |
|||||||||
900 |
36” |
914.40 |
9.53 |
7.92 |
12.70 |
19.05 |
12.70 |
|||||||||
DN 1000mm and above Diameter pipe wall thickness to be customized |
Standard & Grade
Standard |
Steel Grades |
ASTM A312/A312M: Seamless, Welded, and Heavily Cold Worked Austenitic Stainless Steel Pipes |
304, 304L, 310S, 310H, 316, 316L, 321, 321H etc... |
ASTM A269: Seamless and welded austenitic stainless steel tubing for general service |
TP304, TP304L, TP316, TP316L, TP321.TP347 etc... |
ASTM A249: Welded Austenitic Steel Boiler, Superheater, Heat-Exchanger, and Condenser Tubes |
304, 304L, 316, 316L, 316H, 316N, 316LN, 317, 317L, 321, 321H, 347, 347H, 348 |
ASTM A269: Seamless and Welded Stainless Steel Small-Diameter Tubes |
304, 304L, 316, 316L, 316H, 316N, 316LN, 317, 317L, 321, 321H, 347, 347H, 348 |
ASTM A270: Seamless and Welded Austenitic and Ferritic/Austenitic Stainless Steel Sanitary Tubing |
Austenitic Stainless Steel Grades: 304, 304L, 316, 316L, 316H, 316N, 316LN, 317, 317L, 321, 321H, 347, 347H, 348 Ferritic/Austenitic (Duplex) Stainless Steel Grades: S31803, S32205 |
ASTM A358/A358M: Welded Austenitic Steel Pipe Requirements for High-Temperature, High-Pressure, and Corrosive Environments |
304, 304L, 316, 316L, 316H, 316N, 316LN, 317, 317L, 321, 321H, 347, 347H, 348 |
ASTM A554: Welded stainless steel mechanical tubing, commonly used for structural or decorative applications |
304, 304L, 316, 316L |
ASTM A789: Seamless and welded ferritic/austenitic stainless steel tubing for general service |
S31803 (Duplex stainless steel) S32205 (Duplex stainless steel) |
ASTM A790: Seamless and welded ferritic/austenitic stainless steel pipe for general corrosive service, high-temperature service, and duplex stainless steel pipes. |
S31803 (Duplex stainless steel) S32205 (Duplex stainless steel) |
EN 10217-7: welded stainless steel pipes European Standard manufacturing requirements. |
1.4301, 1.4307, 1.4401, 1.4404, 1.4571, 1.4003, 1.4509, 1.4510, 1.4462, 1.4948, 1.4878 etc... |
DIN 17457: German Standard used for manufacturing stainless steel welded pipes |
1.4301, 1.4307, 1.4401, 1.4404, 1.4571, 1.4003, 1.4509, 1.4510, 1.4462, 1.4948, 1.4878 etc... |
JIS G3468: Japanese Industrial Standard that specifies the manufacturing requirements for welded stainless steel pipes. |
SUS304, SUS304L, SUS316, SUS316L, SUS329J3L etc... |
GB/T 12771: Chinese National Standard used for the manufacturing requirements of stainless steel welded pipes. |
06Cr19Ni10, 022Cr19Ni1, 06Cr17Ni12Mo2, 022Cr22Ni5Mo3N |
Austenitic stainless steel:TP304, TP304L, TP304H, TP310S, TP316, TP316L, TP316H, TP316Ti, TP317, TP317L, TP321, TP321H, TP347, TP347H,TP347HFG N08904(904L), S30432, S31254, N08367, S30815...
Duplex stainless steel:S31803, S32205, S32750, S32760, S32707, S32906... Nickel Alloy:N04400, N06600, N06625, N08800, N08810(800H), N08825... Usage: Petroleum, Chemical, Natural gas, Electric power and Mechanical equipment manufacturing industries. |
Quality Control
Raw Material Checking, Chemical Analysis, Mechanical Test, Visual Inspection, Dimension Check, Bend Test, Impact Test, Intergranular Corrosion Test, Non-Destructive Examination(UT, MT, PT) Welding Procedure Qualification, Microstructure Analysis, Flaring and Flattening Test, Hardness Test, Pressure Testing, Ferrite Content Test, Metallography Testing, Corrosion Testing, Eddy Current Testing, Salt Spray Testing, Corrosion Resistance Testing, Vibration Test, Pitting Corrosion Test, Painting and Coating Inspection, Documentation Review…..
Usage & Application
Stainless steel welded pipes find extensive usage across various industries due to their exceptional properties and versatility. These pipes are employed in a wide range of applications, driven by their durability, corrosion resistance, and suitability for diverse environments. Some of the key usage and application areas of stainless steel welded pipes include:
● Industrial Use: Common in oil, gas, petrochemical, and power industries due to corrosion resistance.
● Construction: Used in plumbing, water supply, and structures for their strength and longevity.
● Food Industry: Crucial for conveying food and beverages, meeting hygiene standards.
● Automotive: Employed in exhaust systems and structural parts, enduring tough conditions.
● Medical: Used in medical devices and sanitary piping, prioritizing cleanliness.
● Agriculture: For corrosion-resistant irrigation systems, ensuring efficient water distribution.
● Water Treatment: Suitable for conveying treated and desalinated water.
● Marine: Resistant to saltwater corrosion, widely applied in ships and offshore structures.
● Energy: Transporting fluids in the energy sector, including natural gas and oil.
● Pulp and Paper: Vital for conveying chemicals and fluids in the production process.
In summary, stainless steel welded pipes serve as essential components in a wide array of industries and applications. Their corrosion resistance, mechanical strength, and ability to meet stringent requirements make them indispensable for modern infrastructure, industrial processes, and various specialized sectors.
Packing & Shipping
Stainless steel pipes are packaged and shipped with utmost care to ensure their protection during transit. Here is a description of the packaging and shipping process:
Packaging:
● Protective Coating: Before packaging, stainless steel pipes are often coated with a layer of protective oil or film to prevent surface corrosion and damage.
● Bundling: Pipes of similar sizes and specifications are carefully bundled together. They are secured using straps, ropes, or plastic bands to prevent movement within the bundle.
● End Caps: Plastic or metal end caps are placed on both ends of the pipes to provide additional protection to the pipe ends and threads.
● Padding and Cushioning: Padding materials such as foam, bubble wrap, or corrugated cardboard are used to provide cushioning and prevent impact damage during transportation.
● Wooden Crates or Cases: In some cases, pipes may be packed in wooden crates or cases to provide extra protection against external forces and handling.
Shipping:
● Mode of Transportation: Stainless steel pipes are typically shipped using various modes of transportation such as trucks, ships, or air freight, depending on the destination and urgency.
● Containerization: Pipes may be loaded into shipping containers to ensure safe and organized transit. This also offers protection from weather conditions and external contaminants.
● Labeling and Documentation: Each package is labeled with essential information, including specifications, quantity, handling instructions, and destination details. Shipping documents are prepared for customs clearance and tracking.
● Customs Compliance: For international shipments, all necessary customs documentation is prepared to ensure smooth clearance at the destination.
● Secure Fastening: Within the transportation vehicle or container, pipes are securely fastened to prevent movement and minimize the risk of damage during transit.
● Tracking and Monitoring: Advanced tracking systems may be employed to monitor the location and condition of the shipment in real-time.
● Insurance: Depending on the value of the cargo, shipping insurance may be obtained to cover potential losses or damages during transit.
In summary, stainless steel pipes we produced will be packaged with protective measures and shipped using reliable transportation methods to ensure they reach their destination in optimal condition. Proper packaging and shipping procedures contribute to the integrity and quality of the delivered pipes.
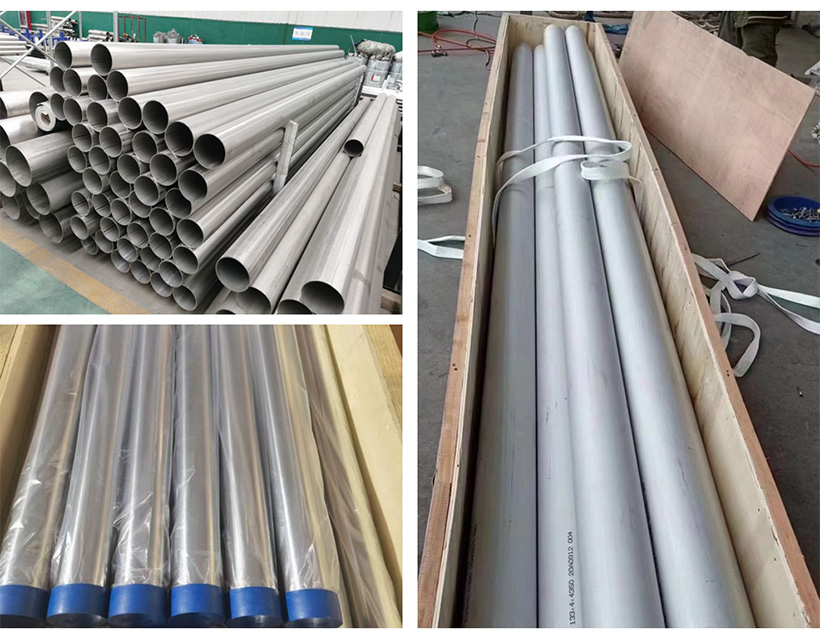