Product Description
LSAW (Longitudinal Submerged Arc Welding) steel pipes are a type of welded steel pipe characterized by their unique manufacturing process and wide range of applications. These pipes are manufactured by forming a steel plate into a cylindrical shape and longitudinally welding it using submerged arc welding techniques. Here is an overview of LSAW steel pipes:
Manufacturing Process:
● Plate Preparation: High-quality steel plates are selected based on specific requirements, ensuring the desired mechanical properties and chemical composition.
● Forming: The steel plate is shaped into a cylindrical pipe through processes like bending, rolling, or pressing (JCOE and UOE). The edges are pre-curved to facilitate welding.
● Welding: Submerged arc welding (SAW) is employed, where an arc is maintained under a flux layer. This produces high-quality welds with minimal defects and excellent fusion.
● Ultrasonic Inspection: After welding, ultrasonic testing is conducted to detect any internal or external defects in the weld zone.
● Expanding: The pipe can be expanded to achieve the desired diameter and wall thickness, enhancing dimensional accuracy.
● Final Inspection: Comprehensive testing, including visual inspection, dimensional checks, and mechanical property tests, ensures the pipe's quality.
Advantages:
● Cost-Efficiency: LSAW pipes offer a cost-effective solution for large-diameter pipelines and structural applications due to their efficient manufacturing process.
● High Strength: The longitudinal welding method results in pipes with strong and uniform mechanical properties.
● Dimensional Accuracy: LSAW pipes exhibit precise dimensions, making them suitable for applications with strict tolerances.
● Weld Quality: Submerged arc welding produces high-quality welds with excellent fusion and minimal defects.
● Versatility: LSAW pipes are used in various industries, including oil and gas, construction, and water supply, owing to their adaptability and durability.
In summary, LSAW steel pipes are manufactured using a precise and efficient process, resulting in versatile, cost-effective, and durable pipes suitable for a wide range of industrial applications.
Specifications
API 5L: GR.B, X42, X46, X52, X56, X60, X65, X70, X80 |
ASTM A252: GR.1, GR.2, GR.3 |
EN 10219-1: S235JRH, S275J0H, S275J2H, S355J0H, S355J2H, S355K2H |
EN10210: S235JRH, S275J0H, S275J2H, S355J0H, S355J2H, S355K2H |
ASTM A53/A53M: GR.A, GR.B |
EN 10217: P195TR1, P195TR2, P235TR1, P235TR2, P265TR1, P265TR2 |
DIN 2458: St37.0, St44.0, St52.0 |
AS/NZS 1163: Grade C250 , Grade C350, Grade C450 |
GB/T 9711: L175, L210, L245, L290, L320 , L360, L390 , L415, L450 , L485 |
ASTMA671: CA55/CB70/CC65, CB60/CB65/CB70/CC60/CC70, CD70/CE55/CE65/CF65/CF70, CF66/CF71/CF72/CF73, CG100/CH100/CI100/CJ100 |
Production Range
Outside Diameter |
Available wall thickness for below steel grade |
|||||||
Inch |
mm |
Steel Grade |
||||||
Inch |
mm |
L245(Gr.B) |
L290(X42) |
L360(X52) |
L415(X60) |
L450(X65) |
L485(X70) |
L555(X80) |
16 |
406 |
6.0-50.0mm |
6.0-48.0mm |
6.0-48.0mm |
6.0-45.0mm |
6.0-40mm |
6.0-31.8mm |
6.0-29.5mm |
18 |
457 |
6.0-50.0mm |
6.0-48.0mm |
6.0-48.0mm |
6.0-45.0mm |
6.0-40mm |
6.0-31.8mm |
6.0-29.5mm |
20 |
508 |
6.0-50.0mm |
6.0-50.0mm |
6.0-50.0mm |
6.0-45.0mm |
6.0-40mm |
6.0-31.8mm |
6.0-29.5mm |
22 |
559 |
6.0-50.0mm |
6.0-50.0mm |
6.0-50.0mm |
6.0-45.0mm |
6.0-43mm |
6.0-31.8mm |
6.0-29.5mm |
24 |
610 |
6.0-57.0mm |
6.0-55.0mm |
6.0-55.0mm |
6.0-45.0mm |
6.0-43mm |
6.0-31.8mm |
6.0-29.5mm |
26 |
660 |
6.0-57.0mm |
6.0-55.0mm |
6.0-55.0mm |
6.0-48.0mm |
6.0-43mm |
6.0-31.8mm |
6.0-29.5mm |
28 |
711 |
6.0-57.0mm |
6.0-55.0mm |
6.0-55.0mm |
6.0-48.0mm |
6.0-43mm |
6.0-31.8mm |
6.0-29.5mm |
30 |
762 |
7.0-60.0mm |
7.0-58.0mm |
7.0-58.0mm |
7.0-48.0mm |
7.0-47.0mm |
7.0-35mm |
7.0-32.0mm |
32 |
813 |
7.0-60.0mm |
7.0-58.0mm |
7.0-58.0mm |
7.0-48.0mm |
7.0-47.0mm |
7.0-35mm |
7.0-32.0mm |
34 |
864 |
7.0-60.0mm |
7.0-58.0mm |
7.0-58.0mm |
7.0-48.0mm |
7.0-47.0mm |
7.0-35mm |
7.0-32.0mm |
36 |
914 |
8.0-60.0mm |
8.0-60.0mm |
8.0-60.0mm |
8.0-52.0mm |
8.0-47.0mm |
8.0-35mm |
8.0-32.0mm |
38 |
965 |
8.0-60.0mm |
8.0-60.0mm |
8.0-60.0mm |
8.0-52.0mm |
8.0-47.0mm |
8.0-35mm |
8.0-32.0mm |
40 |
1016 |
8.0-60.0mm |
8.0-60.0mm |
8.0-60.0mm |
8.0-52.0mm |
8.0-47.0mm |
8.0-35mm |
8.0-32.0mm |
42 |
1067 |
8.0-60.0mm |
8.0-60.0mm |
8.0-60.0mm |
8.0-52.0mm |
8.0-47.0mm |
8.0-35mm |
8.0-32.0mm |
44 |
1118 |
9.0-60.0mm |
9.0-60.0mm |
9.0-60.0mm |
9.0-52.0mm |
9.0-47.0mm |
9.0-35mm |
9.0-32.0mm |
46 |
1168 |
9.0-60.0mm |
9.0-60.0mm |
9.0-60.0mm |
9.0-52.0mm |
9.0-47.0mm |
9.0-35mm |
9.0-32.0mm |
48 |
1219 |
9.0-60.0mm |
9.0-60.0mm |
9.0-60.0mm |
9.0-52.0mm |
9.0-47.0mm |
9.0-35mm |
9.0-32.0mm |
52 |
1321 |
9.0-60.0mm |
9.0-60.0mm |
9.0-60.0mm |
9.0-52.0mm |
9.0-47.0mm |
9.0-35mm |
9.0-32.0mm |
56 |
1422 |
10.0-60.0mm |
10.0-60.0mm |
10.0-60.0mm |
10.0-52mm |
10.0-47.0mm |
10.0-35mm |
10.0-32.0mm |
60 |
1524 |
10.0-60.0mm |
10.0-60.0mm |
10.0-60.0mm |
10.0-52mm |
10.0-47.0mm |
10.0-35mm |
10.0-32.0mm |
64 |
1626 |
10.0-60.0mm |
10.0-60.0mm |
10.0-60.0mm |
10.0-52mm |
10.0-47.0mm |
10.0-35mm |
10.0-32.0mm |
68 |
1727 |
10.0-60.0mm |
10.0-60.0mm |
10.0-60.0mm |
10.0-52mm |
10.0-47.0mm |
10.0-35mm |
10.0-32.0mm |
72 |
1829 |
10.0-60.0mm |
10.0-60.0mm |
10.0-60.0mm |
10.0-52mm |
10.0-47.0mm |
10.0-35mm |
10.0-32.0mm |
* Other Size can be customized after negotiation
Chemical Composition and Mechanical Properties of LSAW Steel Pipe
Standard | Grade | Chemical Composition(max)% | Mechanical Properties(min) | |||||
C | Mn | Si | S | P | Yield Strength(Mpa) | Tensile Strength(Mpa) | ||
GB/T700-2006 | A | 0.22 | 1.4 | 0.35 | 0.050 | 0.045 | 235 | 370 |
B | 0.2 | 1.4 | 0.35 | 0.045 | 0.045 | 235 | 370 | |
C | 0.17 | 1.4 | 0.35 | 0.040 | 0.040 | 235 | 370 | |
D | 0.17 | 1.4 | 0.35 | 0.035 | 0.035 | 235 | 370 | |
GB/T1591-2009 | A | 0.2 | 1.7 | 0.5 | 0.035 | 0.035 | 345 | 470 |
B | 0.2 | 1.7 | 0.5 | 0.030 | 0.030 | 345 | 470 | |
C | 0.2 | 1.7 | 0.5 | 0.030 | 0.030 | 345 | 470 | |
BS EN10025 | S235JR | 0.17 | 1.4 | - | 0.035 | 0.035 | 235 | 360 |
S275JR | 0.21 | 1.5 | - | 0.035 | 0.035 | 275 | 410 | |
S355JR | 0.24 | 1.6 | - | 0.035 | 0.035 | 355 | 470 | |
DIN 17100 | ST37-2 | 0.2 | - | - | 0.050 | 0.050 | 225 | 340 |
ST44-2 | 0.21 | - | - | 0.050 | 0.050 | 265 | 410 | |
ST52-3 | 0.2 | 1.6 | 0.55 | 0.040 | 0.040 | 345 | 490 | |
JIS G3101 | SS400 | - | - | - | 0.050 | 0.050 | 235 | 400 |
SS490 | - | - | - | 0.050 | 0.050 | 275 | 490 | |
API 5L PSL1 | A | 0.22 | 0.9 | - | 0.03 | 0.03 | 210 | 335 |
B | 0.26 | 1.2 | - | 0.03 | 0.03 | 245 | 415 | |
X42 | 0.26 | 1.3 | - | 0.03 | 0.03 | 290 | 415 | |
X46 | 0.26 | 1.4 | - | 0.03 | 0.03 | 320 | 435 | |
X52 | 0.26 | 1.4 | - | 0.03 | 0.03 | 360 | 460 | |
X56 | 0.26 | 1.1 | - | 0.03 | 0.03 | 390 | 490 | |
X60 | 0.26 | 1.4 | - | 0.03 | 0.03 | 415 | 520 | |
X65 | 0.26 | 1.45 | - | 0.03 | 0.03 | 450 | 535 | |
X70 | 0.26 | 1.65 | - | 0.03 | 0.03 | 585 | 570 |
Standard & Grade
Standard |
Steel Grades |
API 5L: Specification for Line Pipe |
GR.B, X42, X46, X52, X56, X60, X65, X70, X80 |
ASTM A252: Standard Specification for Welded and Seamless Steel Pipe Piles |
GR.1, GR.2, GR.3 |
EN 10219-1: Cold Formed Welded Structural Hollow Sections of Non-alloy and Fine Grain Steels |
S235JRH, S275J0H, S275J2H, S355J0H, S355J2H, S355K2H |
EN10210: Hot Finished Structural Hollow Sections of Non-Alloy and Fine Grain Steels |
S235JRH, S275J0H, S275J2H, S355J0H, S355J2H, S355K2H |
ASTM A53/A53M: Pipe, Steel, Black and Hot-Dipped, Zinc-Coated, Welded and Seamless |
GR.A, GR.B |
EN10208: Steel pipes for use in pipeline transportation systems in the petroleum and natural gas industries. |
L210GA, L235GA, L245GA, L290GA, L360GA |
EN 10217: Welded Steel Tubes for Pressure Purposes |
P195TR1, P195TR2, P235TR1, P235TR2, P265TR1, P265TR2 |
DIN 2458: Welded Steel Pipes and Tubes |
St37.0, St44.0, St52.0 |
AS/NZS 1163: Australian/New Zealand Standard for Cold-formed Structural Steel Hollow Sections |
Grade C250 , Grade C350, Grade C450 |
GB/T 9711: Petroleum and Natural Gas Industries - Steel Pipe for Pipelines |
L175, L210, L245, L290, L320 , L360, L390 , L415, L450 , L485 |
ASTM A671: Electric-Fusion-Welded Steel Pipe for Atmospheric and Lower Temperatures |
CA 55, CB 60, CB 65, CB 70, CC 60, CC 65, CC 70 |
ASTM A672: Electric-fusion-welded steel pipe for high-pressure service at moderate temperatures. |
A45, A50, A55, B60, B65, B70, C55, C60, C65 |
ASTM A691: Carbon and alloy steel pipe, electric-fusion-welded for high-pressure service at high temperatures. |
CM-65, CM-70, CM-75, 1/2CR-1/2MO, 1CR-1/2MO, 2-1/4CR, 3CR |
Manufacturing Process
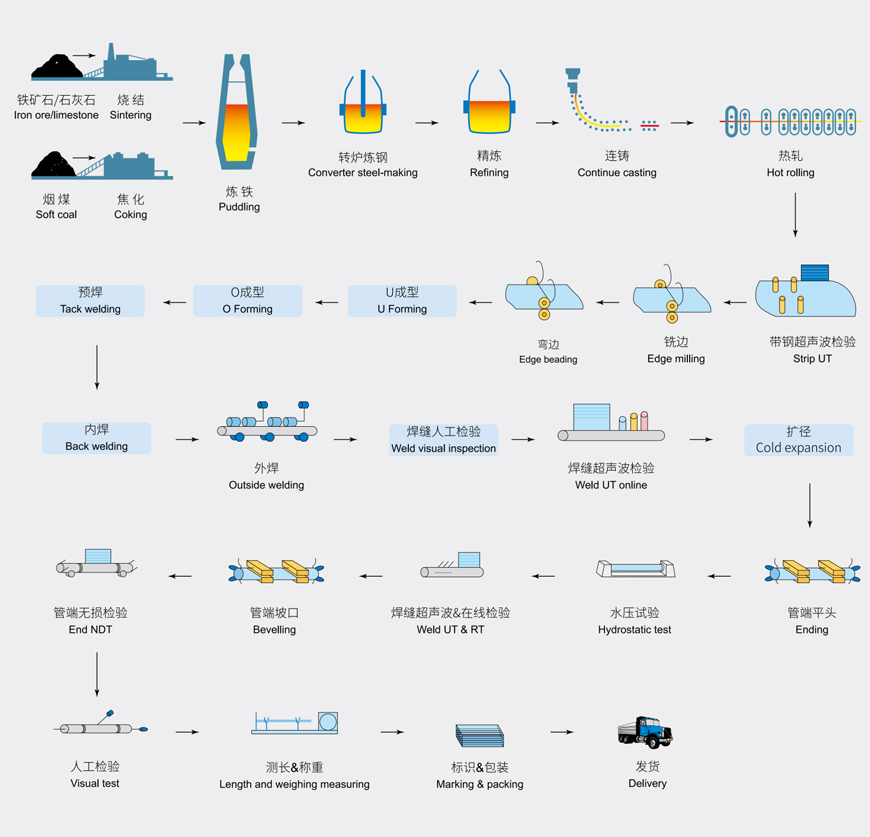
Quality Control
● Raw Material Checking
● Chemical Analysis
● Mechanical Test
● Visual Inspection
● Dimension Check
● Bend Test
● Impact Test
● Intergranular Corrosion Test
● Non-Destructive Examination (UT, MT, PT)
● Welding Procedure Qualification
● Microstructure Analysis
● Flaring and Flattening Test
● Hardness Test
● Hydrostatic Test
● Metallography Testing
● Hydrogen Induced Cracking Test (HIC)
● Sulfide Stress Cracking Test (SSC)
● Eddy Current Testing
● Painting and Coating Inspection
● Documentation Review
Usage & Application
LSAW (Longitudinal Submerged Arc Welding) steel pipes find diverse applications across various industries due to their structural integrity and versatility. Below are some of the key usages and applications of LSAW steel pipes:
● Oil and Gas Transportation: LSAW steel pipes are extensively used in the oil and gas industry for pipeline systems. These pipes are employed for the transportation of crude oil, natural gas, and other fluids or gases.
● Water Infrastructure: LSAW pipes are utilized in water-related infrastructure projects, including water supply and drainage systems.
● Chemical Processing: LSAW pipes serve in chemical industries where they are employed for conveying chemicals, liquids, and gases in a secure and efficient manner.
● Construction and Infrastructure: These pipes are used in various construction projects, such as building foundations, bridges, and other structural applications.
● Piling: LSAW pipes are employed in piling applications to provide foundational support in construction projects, including building foundations and marine structures.
● Energy Sector: They are used for transporting various forms of energy, including steam and thermal fluids in power generation plants.
● Mining: LSAW pipes find application in mining projects for conveying materials and tailings.
● Industrial Processes: Industries such as manufacturing and production utilize LSAW pipes for different industrial processes, including conveying raw materials and finished products.
● Infrastructure Development: These pipes are essential in developing infrastructure projects such as roads, highways, and underground utilities.
● Structural Support: LSAW pipes are used for fabricating structural supports, columns, and beams in construction and engineering projects.
● Shipbuilding: In the shipbuilding industry, LSAW pipes are employed for constructing various parts of ships, including hulls and structural components.
● Automotive Industry: LSAW pipes can be used in the manufacturing of automotive components, including exhaust systems.
These applications demonstrate the versatility of LSAW steel pipes across different sectors, owing to their durability, strength, and suitability for various environmental conditions.
Packing & Shipping
Proper packing and shipping of LSAW (Longitudinal Submerged Arc Welding) steel pipes are crucial to ensure their safe transportation and delivery to various destinations. Here is a description of the typical packing and shipping procedures for LSAW steel pipes:
Packing:
● Bundling: LSAW pipes are often bundled together or Single Piece packed using steel straps or bands to create manageable units for handling and transportation.
● Protection: Pipe ends are protected with plastic caps to prevent damage during transit. Additionally, pipes can be covered with protective material to safeguard against environmental factors.
● Anti-Corrosion Coating: If the pipes have an anti-corrosion coating, the coating's integrity is ensured during packing to prevent damage during handling and transportation.
● Marking and Labeling: Each bundle is labeled with essential information such as pipe size, material grade, heat number, and other specifications for easy identification.
● Securing: Bundles are securely fastened to pallets or skids to prevent movement during transportation.
Shipping:
● Transportation Modes: LSAW steel pipes can be shipped using various modes of transportation, including road, rail, sea, or air, depending on the destination and urgency.
● Containerization: Pipes can be shipped in containers for added protection, especially during overseas transport. Containers are loaded and secured to prevent shifting during transit.
● Logistics Partners: Reputable logistics companies or carriers experienced in handling steel pipes are engaged to ensure safe and timely delivery.
● Customs Documentation: Necessary customs documentation, including bills of lading, certificates of origin, and other relevant paperwork, is prepared and submitted for international shipments.
● Insurance: Depending on the value and nature of the cargo, insurance coverage may be arranged to safeguard against unforeseen events during transit.
● Tracking: Modern tracking systems allow both the sender and receiver to track the progress of the shipment in real-time, ensuring transparency and timely updates.
● Delivery: Pipes are unloaded at the destination, following proper unloading procedures to avoid damage.
● Inspection: Upon arrival, pipes may undergo inspection to verify their condition and conformity to specifications before being accepted by the recipient.
Proper packing and shipping practices help prevent damage, maintain the integrity of LSAW steel pipes, and ensure that they reach their intended destinations safely and in optimal condition.
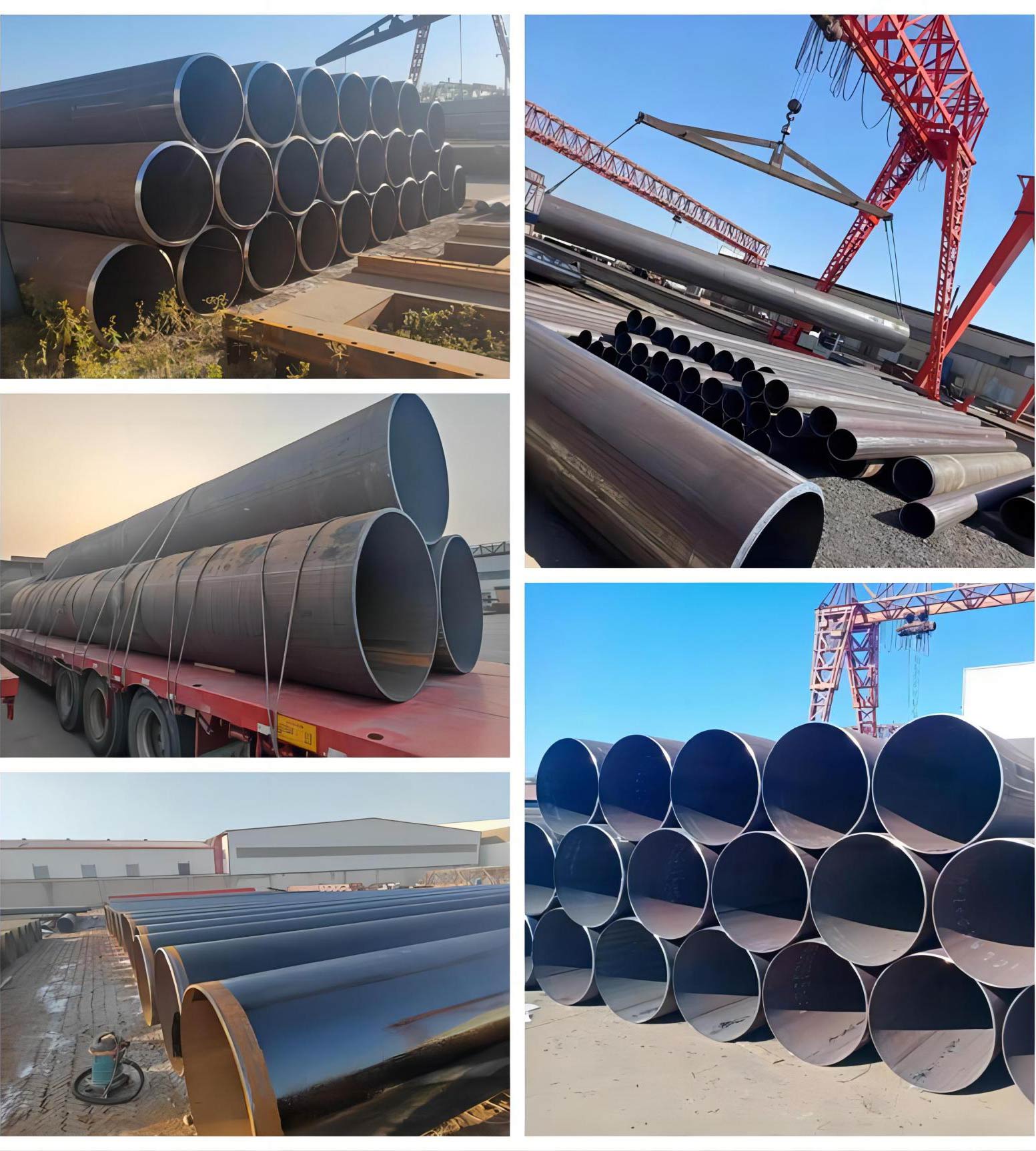