Development history of seamless steel pipe
Seamless steel pipe production has a history of nearly 100 years. The German Mannesmann brothers first invented the two roll cross rolling piercer in 1885, and the periodic pipe mill in 1891. In 1903, the Swiss R.C. stiefel invented the automatic pipe mill (also known as the top pipe mill). After that, various extension machines such as continuous pipe mill and pipe jacking machine appeared, which began to form the modern seamless steel pipe industry. In the 1930s, due to the use of three roll pipe rolling mill, extruder and periodic cold rolling mill, the variety and quality of steel pipes were improved. In the 1960s, due to the improvement of continuous pipe mill and the emergence of three roll piercer, especially the success of tension reducing mill and continuous casting billet, the production efficiency was improved and the competitiveness between seamless pipe and welded pipe was enhanced. In the 1970s, seamless pipe and welded pipe were keeping pace, and the world steel pipe output increased at a rate of more than 5% per year. Since 1953, China has attached importance to the development of seamless steel pipe industry, and has initially formed a production system for rolling all kinds of large, medium and small pipes. Generally, copper pipe also adopts the processes of billet cross rolling and piercing.
Application and classification of seamless steel pipe
Application:
Seamless steel pipe is a kind of economic section steel, which plays a very important role in the national economy. It is widely used in petroleum, chemical industry, boiler, power station, ship, machinery manufacturing, automobile, aviation, aerospace, energy, geology, construction, military industry and other departments.
Classification:
① According to the section shape: circular section pipe and special section pipe.
② according to the material: carbon steel pipe, alloy steel pipe, stainless steel pipe and composite pipe.
③ according to the connection mode: threaded connection pipe and welded pipe.
④ according to the production mode: hot rolling (extrusion, jacking and expansion) pipe and cold rolling (drawing) pipe.
⑤ according to the purpose: boiler pipe, oil well pipe, pipeline pipe, structural pipe and chemical fertilizer pipe.
Production technology of seamless steel pipe
① Main production process (main inspection process) of hot rolled seamless steel pipe:
Tube blank preparation and inspection → tube blank heating → perforation → tube rolling → reheating of raw tube → sizing (reducing) → heat treatment → straightening of finished tube → finishing → inspection (nondestructive, physical and chemical, bench test) → warehousing.
② Main production processes of cold rolled (drawn) seamless steel pipe
Blank preparation → pickling and lubrication → cold rolling (drawing) → heat treatment → straightening → finishing → inspection.
The production process flow chart of hot rolled seamless steel pipe is as follows:
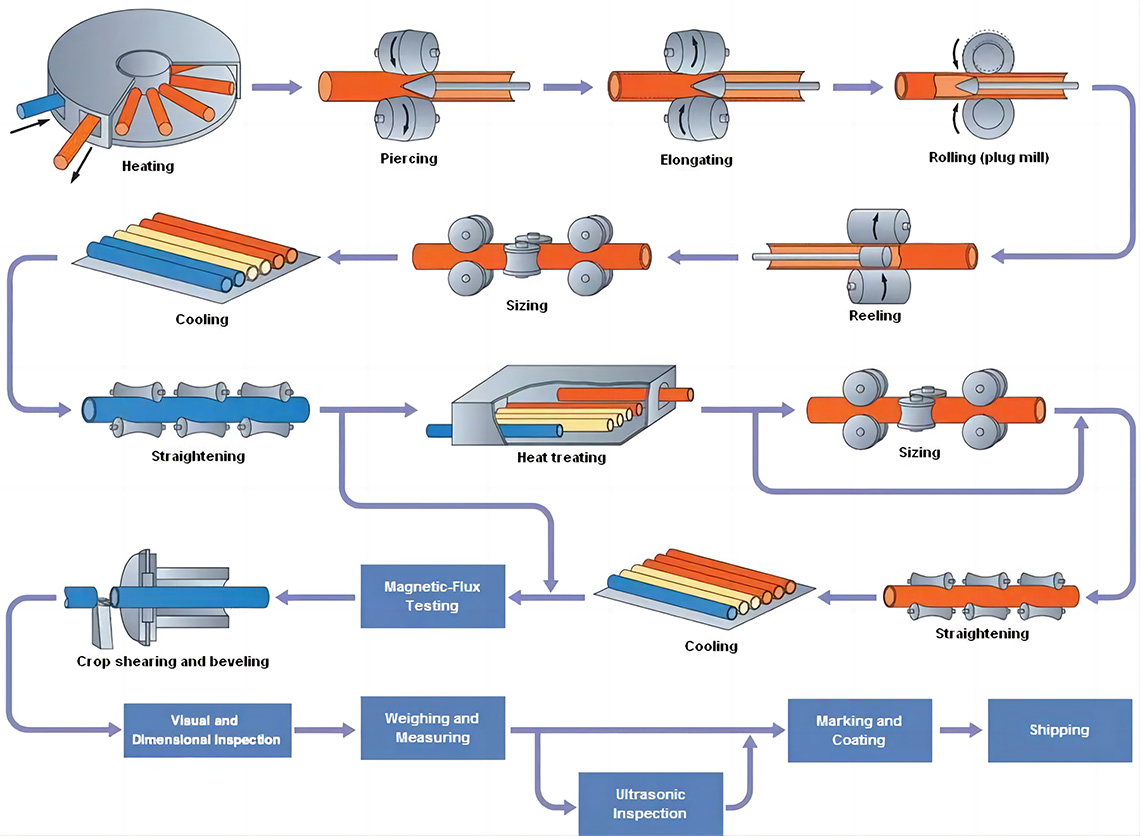
Post time: Sep-14-2023