Corrosion is the destruction or deterioration of materials or their properties caused by the environment. Most corrosion occurs in atmospheric environments, which contain corrosive components and corrosive factors such as oxygen, humidity, temperature changes and pollutants.
Cyclic Corrosion is a common and most destructive atmospheric corrosion. Cyclic Corrosion corrosion on the surface of metal materials is due to the chloride ions contained in the metal surface of the oxidized layer and the protective layer of the metal surface penetration and the internal metal electrochemical reaction caused by. At the same time, chlorine ions contain a certain hydration energy, easy to be adsorbed in the pores of the metal surface, cracks crowded and replace the oxygen in the oxide layer, insoluble oxides into soluble chlorides, so that the passivation of the state of the surface into an active surface.
Cyclic Corrosion test is a kind of environmental test mainly using Cyclic Corrosion test equipment to create artificial simulation of Cyclic Corrosion environmental conditions to assess the corrosion resistance of products or metal materials. It is divided into two categories, one for the natural environment exposure test, the other for the artificial accelerated simulation of Cyclic Corrosion environment test.
Artificial simulation of Cyclic Corrosion environmental testing is the use of a certain volume of space test equipment - Cyclic Corrosion test chamber (Figure), in its volume of space with artificial methods, resulting in a Cyclic Corrosion environment to assess the quality of the product's Cyclic Corrosion corrosion resistance.
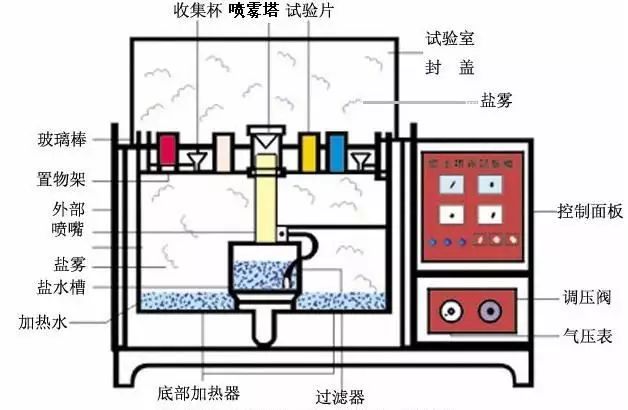
It is compared with the natural environment, the salt concentration of chloride of its Cyclic Corrosion environment, can be several times or dozens of times the general natural environment Cyclic Corrosion content, so that the corrosion rate is greatly increased, the Cyclic Corrosion test on the product, the time to get the results is also greatly shortened. Such as in the natural exposure environment for a product sample test, to be its corrosion may take 1 year, while in the artificial simulation of Cyclic Corrosion environmental conditions, as long as 24 hours, you can get similar results.
Laboratory simulated Cyclic Corrosion can be divided into four categories
(1) Neutral Cyclic Corrosion Test (NSS test) is an accelerated corrosion test method that appeared the earliest and is currently the most widely used. It uses 5% sodium chloride saline solution, solution PH value adjusted in the neutral range (6.5 ~ 7.2) as a solution for spraying. The test temperature are taken 35 ℃, the settlement rate of the Cyclic Corrosion requirements in 1 ~ 2ml/80cm / h.
(2) Acetic acid Cyclic Corrosion test (ASS test) is developed on the basis of neutral Cyclic Corrosion test. It is to add some glacial acetic acid in 5% sodium chloride solution, so that the PH value of the solution is reduced to about 3, the solution becomes acidic, and the final formation of Cyclic Corrosion is also changed from neutral Cyclic Corrosion to acidic. Its corrosion rate is about 3 times faster than NSS test.
(3) Copper salt accelerated acetic acid Cyclic Corrosion test (CASS test) is a newly developed foreign rapid Cyclic Corrosion test, the test temperature of 50 ℃, salt solution with a small amount of copper salt - copper chloride, strongly induced corrosion. Its corrosion rate is about 8 times that of the NSS test.
(4)Alternating Cyclic Corrosion test is a comprehensive Cyclic Corrosion test, which is actually neutral Cyclic Corrosion test plus constant humidity and heat test. It is mainly used for cavity-type whole products, through the penetration of the humid environment, so that the Cyclic Corrosion is not only generated on the surface of the product, but also inside the product. It is the product in the Cyclic Corrosion and humid heat two environmental conditions alternately, and finally assess the electrical and mechanical properties of the whole product with or without changes.
The test results of Cyclic Corrosion testing are generally given in qualitative rather than quantitative form. There are four specific judgment methods.
① rating judgment method is the corrosion area and the total area of the ratio of the percentage according to a certain method of division into several levels, to a certain level as a qualified judgment basis, it is suitable for flat samples for evaluation.
② weighing judgment method is through the weight of the sample before and after the corrosion test weighing method, calculate the weight of the loss of corrosion to judge the quality of the sample corrosion resistance, it is particularly suitable for a metal corrosion resistance quality assessment.
③ corrosive appearance determination method is a qualitative determination method, it is Cyclic Corrosion test, whether the product produces corrosion phenomenon to determine the sample, general product standards are mostly used in this method.
④ corrosion data statistical analysis method provides the design of corrosion tests, analysis of corrosion data, corrosion data to determine the confidence level of the method, which is mainly used to analyze, statistical corrosion, rather than specifically for a specific product quality judgment.
Cyclic Corrosion testing of stainless steel
Cyclic Corrosion test was invented in the early twentieth century, is the longest use of the "corrosion test", highly corrosion-resistant materials user's favor, has become a "universal" test. The main reasons are as follows: ① time-saving; ② low cost; ③ can test a variety of materials; ④ the results are simple and clear, favorable to the settlement of commercial disputes.
In practice, the Cyclic Corrosion test of stainless steel is the most widely known - how many hours can this material Cyclic Corrosion test? Practitioners must be no stranger to this question.
Material vendors usually use passivation treatment or improve the surface polishing grade, etc., to improve the Cyclic Corrosion test time of stainless steel. However, the most critical determining factor is the composition of the stainless steel itself, i.e. the content of chromium, molybdenum and nickel.
The higher the content of the two elements, chromium and molybdenum, the stronger the corrosion performance needed to resist pitting and crevice corrosion beginning to appear. This corrosion resistance is expressed in terms of the so-called Pitting Resistance Equivalent (PRE) value: PRE = %Cr + 3.3 x %Mo.
Although nickel does not increase the resistance of steel to pitting and crevice corrosion, it can effectively slow down the corrosion rate after the corrosion process has started. Nickel-containing austenitic stainless steels therefore tend to perform much better in Cyclic Corrosion tests, and corrode much less severely than low-nickel ferritic stainless steels with similar resistance to pitting corrosion equivalents
Trivia: For standard 304, neutral Cyclic Corrosion is generally between 48 and 72 hours; for standard 316, neutral Cyclic Corrosion is generally between 72 and 120 hours.
It should be noted that the Cyclic Corrosion test has major drawbacks when testing the properties of stainless steel. The chloride content of the Cyclic Corrosion in the Cyclic Corrosion test is extremely high, far exceeding the real environment, so the stainless steel that can resist corrosion in the actual application environment with a very low chloride content will also be corroded in the Cyclic Corrosion test.
Cyclic Corrosion test changes the corrosion behavior of stainless steel, it can neither be regarded as an accelerated test nor a simulation experiment. The results are one-sided and have no equivalent relationship with the actual performance of the stainless steel that is finally put into use.
So we can use the Cyclic Corrosion test to compare the corrosion resistance of different types of stainless steel, but this test is only able to rate the material. When selecting stainless steel materials specifically, the Cyclic Corrosion test alone does not usually provide sufficient information, because we do not have a sufficient understanding of the link between the test conditions and the actual application environment.
For the same reason, it is not possible to estimate the service life of a product based solely on the Cyclic Corrosion test of a stainless steel sample.
In addition, it is not possible to make comparisons between different types of steel, for example, we cannot compare stainless steel with coated carbon steel, because the corrosion mechanisms of the two materials used in the test are very different, and the correlation between the test results and the actual environment in which the product will end up being used is not the same.

Post time: Nov-06-2023