What is a flange?
Flange for short, just a general term, usually refers to a similar disk-shaped metal body to open a few fixed holes, used to connect other things, this kind of thing is widely used in machinery, so it looks a little strange, as long as it is known as a flange, its name is derived from the English flange. so that the pipe and the pipe interconnection of parts, connected to the end of the pipe, the flange has an aperture, screws to make the two flanges Tightly connected, between the flange with a gasket seal.
Flange is a disk-shaped parts, the most common in pipeline engineering, flange are used in pairs.
Regarding the types of flange connections, there are three components:
- Pipe flanges
- Gasket
- Bolt connection
In most cases, there is a specific gasket and bolt material found that is made from the same material as the pipe flange component. The most common flanges are stainless steel flanges. Flanges, on the other hand, are available in a variety of materials in order to match them to the requirements of the site. Some of the most common flange materials are monel, inconel, and chrome molybdenum, depending on the actual site requirements. The best choice of material should depend on the type of system in which you wish to use a flange with specific requirements.
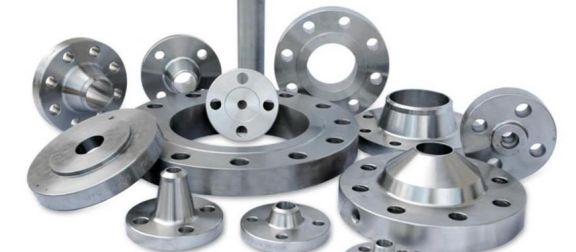
7 Common Types of Flanges
There are various types of flanges that can be selected according to the requirements of the site. To match the design of the ideal flange, reliable operation as well as long service life must be ensured and the most suitable price should be considered.
1. threaded flange:
Threaded flanges, which have a thread in the flange bore, are fitted with external threads on the fitting. Threaded connection is here meant to avoid welding in all cases. It is mainly connected by matching threads with the pipe to be installed.
2. Socket weld flanges
This type of flange is usually used for smaller pipes where the diameter of the low temperature and low pressure region is characterized by a connection in which the pipe is placed inside the flange to ensure a connection with a single or multi-route fillet weld. This avoids the constraints associated with threaded ends as compared to other welded flange types, thus making installation simple.
3. Lap flanges
A lap flange is a type of flange that requires the stub end to be butt-welded to a fitting in order to be used with a support flange to form a flanged connection. This design has made this method popular in a variety of systems where physical space is limited, or where frequent disassembly is required, or where a high degree of maintenance is required.
4. Sliding flanges
Sliding flanges are very common and are available in a wide range of sizes to suit systems with high flow rates and throughputs. Simply matching the flange to the outside diameter of the pipe makes the connection very easy to install. Installation of these flanges is a bit technical as it requires fillet welding on both sides to secure the flange to the pipe.
5. Blind flanges
These types of flanges are well suited for the termination of piping systems. The blind plate is shaped like a blank disk that can be bolted. Once these are properly installed and combined with the correct gasket, it allows for an excellent seal and is easy to remove when needed.
6. Weld Neck Flanges
Weld neck flanges are very similar to lap flanges, but require butt welding for installation. And the integrity of this system's performance and its ability to be bent many times over and used in high pressure and high temperature systems makes it the primary choice for process piping.
7. Specialty flanges
This type of flange is the most familiar. However, there is a wide range of additional specialized flange types available to suit a variety of uses and environments. There are various other options such as nipo flanges, weldo flanges, expansion flanges, orifices, long weld necks and reducer flanges.
5 Special Types of Flanges
1. Weldo Flange
Weldo flange is very similar to Nipo flange as it is a combination of butt-welding flanges and branch fitting connections. Weldo flanges are made from a single piece of solid forged steel, rather than individual parts being welded together.
2. Nipo flange
Nipoflange is a branch pipe inclined at an angle of 90 degrees, it is a product manufactured by combining butt-welding flanges and forged Nipolet. While Nipo flange is found to be a sturdy single piece of forged steel, it is not understood to be two different products welded together.Installation of Nipoflange consists of welding to the Nipolet portion of the equipment in order to run the pipe and bolting the flange portion to the stub pipe flange by the piping crew.
It is important to know that Nipo flanges are available in various types of materials such as carbon, high and low temperature carbon steels, stainless steel grades, and nickel alloys.Nipo flanges are mostly made with reinforced fabrication, which helps to give them extra mechanical strength when compared to standard Nipo flange.
3. Elboflange and Latroflange
Elboflange is known as a combination of flange and Elbolet while Latroflange is known as a combination of flange and Latrolet. Elbow flanges are used to branch pipes at a 45 degree angle.
4. Swivel ring flanges
The application of swivel ring flanges is to facilitate the alignment of bolt holes between two paired flanges, which is more helpful in many situations, such as the installation of large diameter pipelines, submarine or offshore pipelines and similar environments. These types of flanges are suitable for demanding fluids in oil, gas, hydrocarbons, water, chemicals and other petrochemical and water management applications.
In the case of large diameter pipelines, the pipe is fitted with a standard butt weld flange at one end and a swivel flange at the other. This works by simply rotating the swivel flange on the pipeline so that the operator achieves proper alignment of the bolt holes in a very easy and faster manner.
Some of the major standards for swivel ring flanges are ASME or ANSI, DIN, BS, EN, ISO, and others. One of the most popular standards for petrochemical applications is ANSI or ASME B16.5 or ASME B16.47. Swivel flanges are flanges that can be used in all common flange standard shapes. For example, weld necks, slip ons, lap joints, socket welds, etc., in all material grades, in a wide range of sizes from 3/8" to 60", and pressures from 150 to 2500. these flanges can be easily fabricated from carbon, alloy, and stainless steels.
5. Expansion flanges
Expansion flanges, are used to increase the bore size of a pipe from any particular point to another in order to connect the pipe to any other mechanical equipment such as pumps, compressors, and valves that are found to have different inlet sizes.
Expansion flanges are usually butt-welded flanges that have a very large hole at the non-flanged end. It can be used to add just one or two sizes or up to 4 inches to the running pipe bore. These types of flanges are preferred over the combination of butt-weld reducers and standard flanges because they are cheaper and lighter. One of the most common materials used for expansion flanges is A105 and stainless steel ASTM A182.
Expansion flanges are available in pressure ratings and sizes in accordance with ANSI or ASME B16.5 specifications, which are primarily available convex or flat (RF or FF). Reducing flanges, also known as reducing flanges, serve the exact opposite function compared to expansion flanges, meaning they are used to reduce the bore size of a pipe. The bore diameter of a run of pipe can be easily reduced, but not by more than 1 or 2 sizes. If an attempt is made to reduce beyond this, a solution based on a combination of butt-welded reducers and standard flanges should be used.
Flange Sizing and Common Considerations
In addition to the functional design of a flange, its size is the factor most likely to influence flange selection when designing, maintaining and updating a piping system. Instead, consideration must be given to the flange's interface with the pipe and the gaskets used to ensure proper sizing. In addition to this, some common considerations are as follows:
- Outer diameter: The outer diameter is the distance between two opposite edges of the flange face.
- Thickness: The thickness is measured from the outside of the rim.
- Bolt Circle Diameter: This is the distance between the relative bolt holes measured from center to center.
- Pipe Size: The pipe size is the size corresponding to the flange.
- Nominal Bore: The nominal bore is the size of the inside diameter of the flange connector.
Flange Classification and Service Level
Flanges are categorized primarily by their ability to withstand different temperatures and pressures. It is designated by the use of letters or suffixes "#", "lb" or "class". These are interchangeable suffixes and also vary by region or supplier. Common known classifications are listed below:
- 150#
- 300#
- 600#
- 900#
- 1500#
- 2500#
The same pressure and temperature tolerances vary depending on the material used, flange design and flange size. However, the only constant is the pressure rating, which decreases as the temperature increases.
Flange Face Type
Face type is also a very important characteristic that has a significant impact on the final performance and service life of the flange. Therefore, some of the most important types of flange faces are analyzed below:
1. Flat Flange (FF)
The gasket surface of a flat flange is in the same plane as the surface of the bolted frame. Commodities that use flat flanges are usually those that are manufactured with molds to match the flange or flange cover. Flat flanges should not be placed on inverted side flanges.ASME B31.1 states that when joining flat cast iron flanges to carbon steel flanges, the raised face on the carbon steel flanges must be removed and a full face gasket is required. This is to prevent small, brittle cast iron flanges from splashing into the void formed by the raised nose of the carbon steel flange.
This type of flange face is used in the manufacture of equipment and valves for all applications where cast iron is manufactured. Cast iron is more brittle and is usually used only for low temperature, low pressure applications. The flat face allows both flanges to make complete contact over the entire surface. Flat Flanges (FF) have a contact surface that is the same height as the bolt threads of the flange. Full face washers are used between two flat flanges and are usually soft. According to ASME B31.3, flat flanges should not be mated with elevated flanges due to the potential for leakage from the resulting flanged joint.
2. Raised-Face Flange (RF)
The raised face flange is the most common type used in fabricator applications and is easily recognized. It is called convex because the face of the gasket is located above the face of the bolt ring. Each type of facing requires the use of several types of gaskets, including a variety of flat ring tabs and metal composites such as spiral-wound and double-sheathed forms.
RF flanges are designed to concentrate further pressure on a smaller area of the gasket, thereby improving the pressure control of the joint. diameters and heights by pressure level and diameter are described in ASME B16.5. Flange pressure level specifies the height of the face being lifted.RF flanges are intended to concentrate further pressure on a smaller area of the gasket, thereby increasing the pressure-control capability of the joint.Diameters and heights by pressure class and diameter are described in ASME B16.5. Pressure flange ratings.
3. Ring flange (RTJ)
When a metal-to-metal seal between paired flanges is required (which is the condition for high-pressure and high-temperature applications, i.e., above 700/800 C°), the Ring Joint Flange (RTJ) is used.
The ring joint flange has a circular groove that accommodates the ring joint gasket (oval or rectangular).
When two ring joint flanges are bolted together and then tightened, the applied bolt force deforms the gasket in the groove of the flange, creating a very tight metal-to-metal seal. In order to accomplish this, the material of the ring joint gasket must be softer (more ductile) than the material of the flanges.
RTJ flanges can be sealed with RTJ gaskets of different types (R, RX, BX) and profiles (e.g., octagonal/elliptical for R type).
The most common RTJ gasket is the R type with an octagonal cross-section, as it ensures a very strong seal (oval cross-section is the older type). However, the "flat groove" design accepts both types of RTJ gaskets with an octagonal or oval cross-section.
4. Tongue and groove flanges (T & G)
Two tongue and groove flanges (T & G faces) fit perfectly: one flange has a raised ring and the other has grooves where they fit easily (the tongue goes into the groove and seals the joint).
Tongue and groove flanges are available in large and small sizes.
5. Male and Female Flanges (M & F)
Similar to tongue and groove flanges, male and female flanges (M & F face types) match each other.
One flange has an area that extends beyond its surface area, the male flange, and the other flange has matching depressions machined into the facing surface, the female flange.
Flange Surface Finish
In order to ensure a perfect fit of the flange to the gasket and the mating flange, the flange surface area requires a certain degree of roughness (RF and FF flange finishes only). The type of roughness of the flange face surface defines the type of "flange finish".
Common types are stock, concentric serrated, spiral serrated and smooth flange faces.
There are four basic surface finishes for steel flanges, however, the common goal of any type of flange surface finish is to produce the desired roughness on the flange surface to ensure a solid fit between the flange, gasket and mating flange to provide a quality seal.
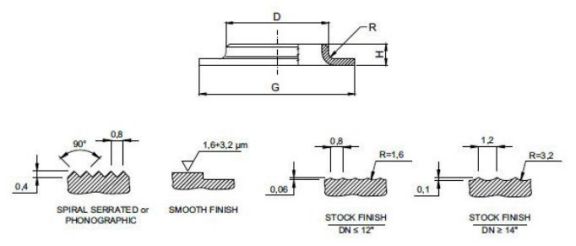
Post time: Oct-08-2023