1. Introduction to Heavy Weight Drill Pipes
Drill pipes are critical components connecting surface equipment to downhole tools. Heavy Weight Drill Pipes (HWDP), as specialized drill pipes, serve as a transitional element between standard drill pipes and drill collars. Through optimized structural design and advanced materials, HWDP plays a vital role in load-bearing, vibration damping, and well trajectory stabilization under complex drilling conditions.
Key Design Features:
Structural Transition: Bridges "flexible" drill pipes and "rigid" drill collars, mitigating stress concentration at junctions.
Enhanced Wall Thickness: 2–3 times thicker than standard drill pipes while maintaining the same outer diameter (e.g., φ50 mm, φ89 mm) for operational compatibility.
Multifunctional Applications: Replaces drill collars in slim-hole drilling, reduces torque and stuck pipe risks in directional wells, and enables precise weight-on-bit (WOB) control.
2. Structural Design: Dual Assurance of Strength and Wear Resistance
2.1 Pipe Body Structure
Upset Design: Internal, external, or combined upset at pipe ends to enhance compression resistance and fatigue performance.
Internal Upset: Maintains outer diameter for narrow wellbores.
External Upset: Boosts axial load capacity for vertical wells.
Combined Upset: Optimal for extreme environments like ultra-deep wells.
Material Selection: High-strength alloys (e.g., 4145H MOD) with yield strengths ranging from 55,000 to 110,000 KSI.
2.2 Tool Joint Technology
Extended Tool Joints: Increase contact area to distribute tension, compression, and torsional loads.
Connection Methods:
Threaded Connections: API or double-shoulder threads with sealants for leak prevention.
Welded Structures: Integral forged joints for high-stress applications.
2.3 Wear-Resistant Hardbanding
Material: Tungsten carbide (HRC ≥60)
Functions:Reduces pipe body wear by 50% in horizontal wells.
Enhances friction for drill string stabilization and trajectory control.
3. Core Functions: From Stress Mitigation to Wellbore Stability
3.1 Stress Buffering
Vibration Absorption: Upset sections and elastic materials convert drill collar vibrations into elastic energy dissipation.
Torque Damping: Extended tool joints redistribute torsional stresses, minimizing fatigue failures in standard pipes.
3.2 WOB Optimization
Weight Advantage: Intermediate weight (e.g., 38 kg/m for φ89 mm HWDP) between drill pipes and collars.
Adaptive Control: Adjusts WOB for shale formations (prevents stuck pipe) and hard-rock layers (enhances penetration).
3.3 Trajectory and Wellbore Integrity
Directional Stability: Hardbanding minimizes drill string wobble, maintaining planned well paths.
Anti-Collapse: Reduces localized pressure spikes from bending, while mud circulation ensures hole cleanliness.
4. Practical Applications
4.1 Ultra-Deep Well Drilling
Case Study: Tashen-1 Well (8,408 m depth, >200°C, 140 MPa pressure).
Performance: High-temperature-resistant alloys and upset designs overcame abrasive formations and cyclic stresses.
4.2 Challenging Geological Conditions
Sour Gas Environments: Jiaoye-1HF Well (Fuling Shale Gas Field) used corrosion-resistant alloys and coatings to combat H₂S.
Directional/Horizontal Wells: Spiral-type HWDP reduced friction and improved directional control.
5. Technological Advancements
5.1 Manufacturing Innovations
Heat Treatment: Quenching and tempering to improve impact toughness.
Quality Assurance: 100% ultrasonic testing (UT) and magnetic particle inspection (MPI).
5.2 Smart Manufacturing
MES/ERP Integration: Full-process traceability from order to delivery.
Customization Options: Double-shoulder connections, extended hardbanding, and internal plastic coatings.
6. Manufacturing Process
Material Selection: 4145H MOD alloy steel bars.
Pipe Processing: Drilling → upset forging → heat treatment.
Tool Joint Fabrication: Forging → thread cold rolling → phosphating.
Welding/Assembly: Friction welding or integral machining.
Quality Control: UT thickness measurement, hardness testing, pressure validation.
Surface Treatment: Hardbanding application and anti-corrosion coatings.
Conclusion
As a cornerstone of modern drilling technology, HWDP combines structural innovation and material science to enhance drilling safety and efficiency. From ultra-deep wells to corrosive formations, its dual role as a "flexible transition" and "rigid support" continues to push the boundaries of oil and gas exploration.
Choose Womic Steel Group as your reliable partner for drill pipes and unbeatable delivery performance. Welcome Inquiry!
Website: www.womicsteel.com
Email: sales@womicsteel.com
Tel/WhatsApp/WeChat: Victor: +86-15575100681 or Jack: +86-18390957568
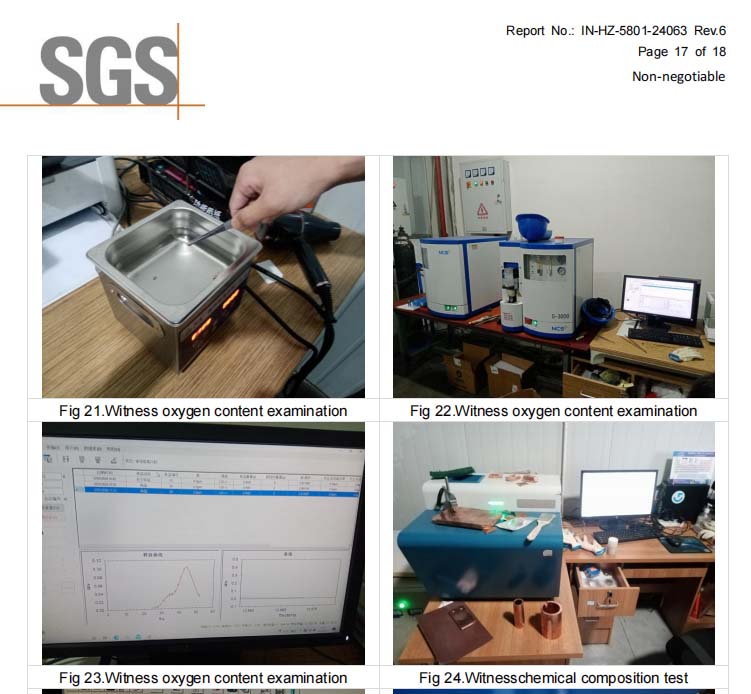
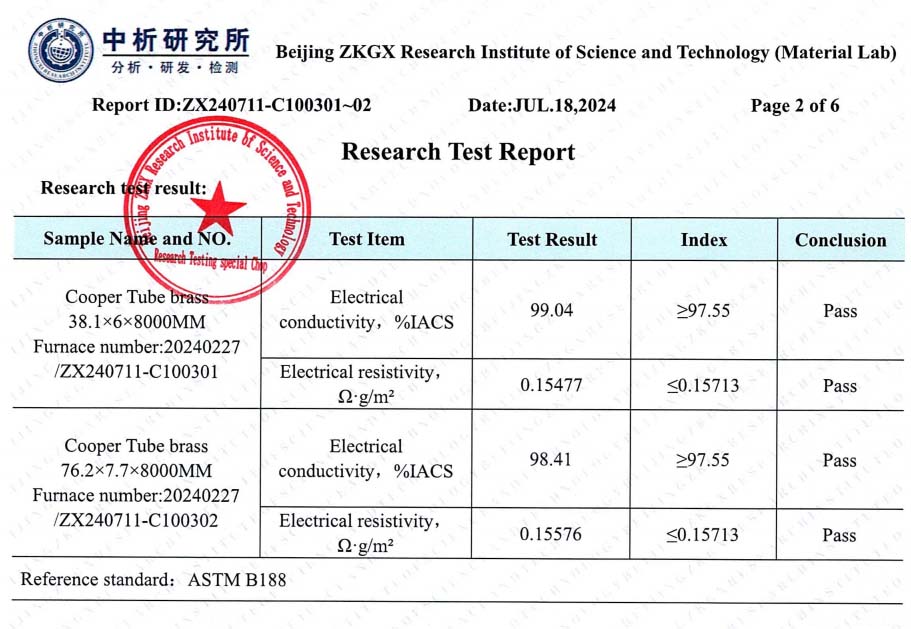
Third-Party Testing:
We fully support inspection by internationally certified bodies such as SGS, TÜV, BV, and DNV, with detailed reports issued prior to delivery.
6. Packaging, Shipping & Factory Service
Womic Copper provides safe, export-grade packaging to protect product quality during domestic or international shipment.
Packaging Features:
● Plastic end caps + individual poly wrap
●Vacuum-sealed PE bags to prevent oxidation
● Fumigated wooden crates with steel band reinforcement
● Each tube labeled with heat number, lot number, and specifications
Transportation:
●Available in FCL, LCL, and air freight
●Logistics service includes CIF, FOB, DDP, and EXW
●Reinforced loading + lashing for long-distance shipment
●Documents prepared for customs, port, and third-party agencies
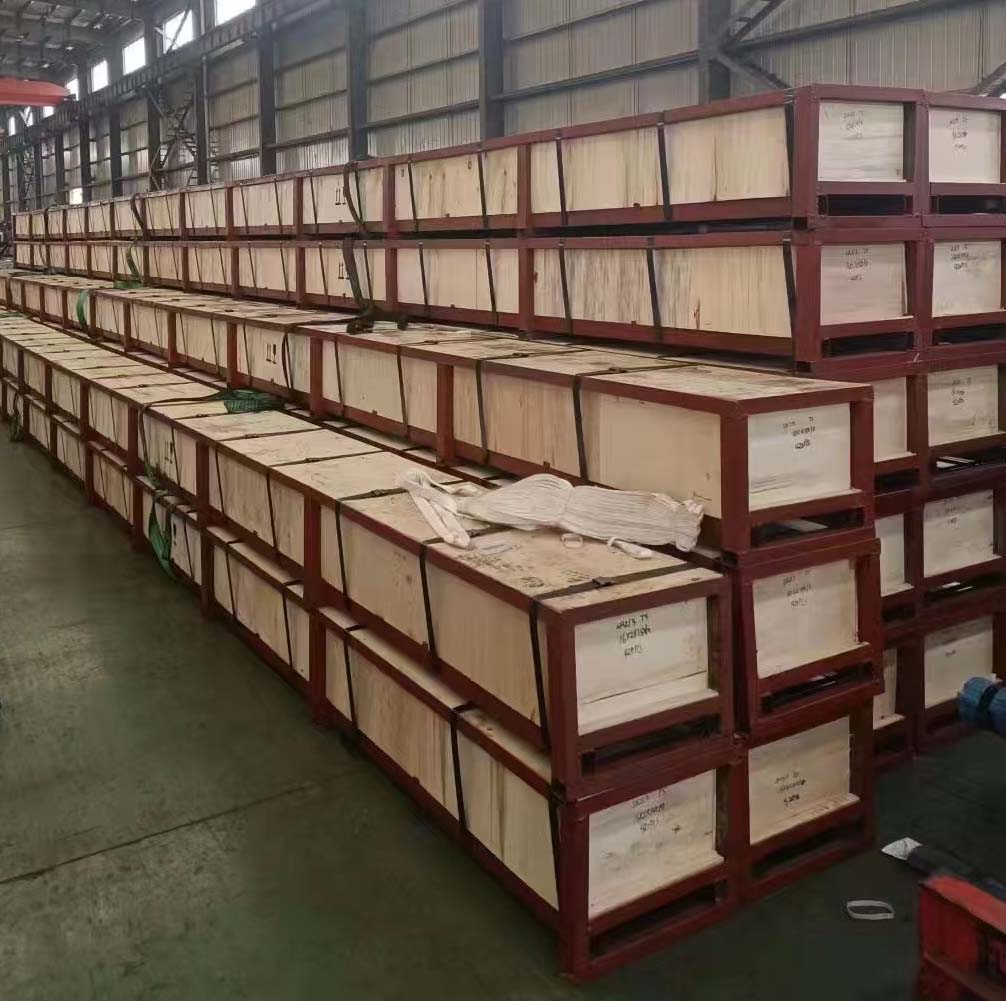
7. Why Choose Womic Copper
●Ultra-Low Oxygen Control – 3–5 ppm oxygen level, industry leading
●Advanced Seamless Production – Full hot + cold drawing, annealing, H80 temper
●100% QC Tracing System – End-to-end digital traceability
●Worldwide Project Experience – Supplied 500kV substation systems in Asia and Europe
●Factory Audit Welcome – On-site inspection, transparent production
● Safe and Global Logistics – On-time delivery with complete documentation
Post time: Apr-11-2025